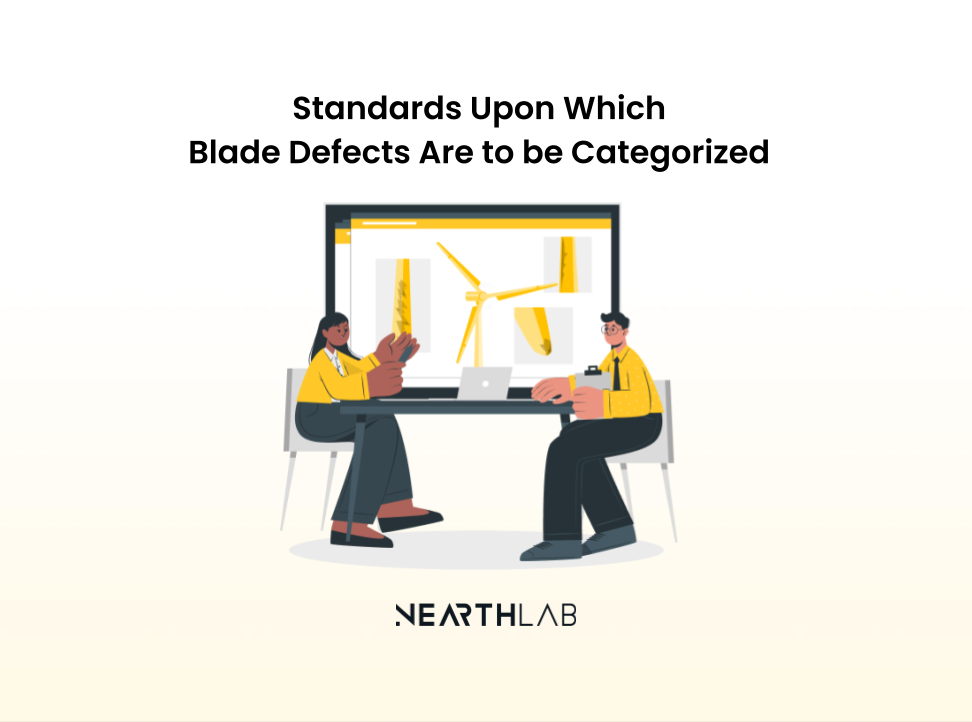
Wind power has blasted to the front of the pack in the race toward a sustainable future. Behind its rapid rise are unsung heroes in rotor blades.
Spinning tirelessly atop majestic wind farms, these colossal yet delicate fiberglass composites battle through repetitive fatigue loads and harsh weather conditions each passing day just to bear the fruits of clean electricity we need to jumpstart the energy transition.
In paying homage to their noble sacrifice, here we embark on a journey to explore the world of blade defects, shedding light on a list of categories into which they fall.
Present State of Affairs
Unless you didn’t know already, the wind industry is yet to see universal standards by which defects are sorted.
There have been attempts to put forward industry-wide categories but to little avail. The reasons are twofold.
First off, the discrepancy between actual and expected wind loads. Blades are designed with maximum pressure in mind. But certain areas may present lower resistance than expected, leaving room for what would’ve downright been a critical defect at sites facing higher velocity to be less of a deal.
Along with wind loads, inconsistency across the supply chain is also in play. Even if suppliers were to work with identical designs and tolerance limits, there’s no viable way to get every production facility to operate under the same manufacturing parameters, such as relative humidity, temperature, and vacuum pressure. These subtle yet distinct contrasts are bound to add up to make notable variations across material properties, which play a big part as to how a blade reacts to changes in surrounding factors and aerodynamic pressure.
New Era of Defect Categorization as Powered by Nearthlab
Case in point – coming up with reasonable standards that can drum up approval from wind farms of all stripes is a tall order. Hence the reason why we, with all humility, take much joy and pride in our latest achievement.
The categories we’re about to list out are a culmination of a decade-long track record of having analyzed a trillion gigabytes worth of post-inspection images. In the process, we’ve helped wind farms around the world – onshore and offshore alike – get the most out of their O&M budgets by setting forth clear-cut benchmarks for making out which defects deserve immediate attention and, vice-versa, which ones don’t.
Before we get down to the sweet science of categorization, let’s quickly brush over the types of damage found across the blades.
- Surface. Standing tall amidst open landscapes and the vast blue ocean, the surface serves as a frontline defense against nature's wrath. Braving rain, hail, and the full heat of the sun, every day remains yet another battle against wear and tear for the coating, tape, and paint encasing the blades.
- Structural. Beneath the sleek exterior belies the brittle core. Once the surface falls and the shell is exposed, that’s when things start spiraling out of control. Chips, cracks, and erosion on the laminate and bonding must be tended to in due course, if not right away.
- Add-on. Blades these days are equipped with accessory devices that function as a buffer against devastating extraneous circumstances like lightning. Keeping them in working order isn’t to be taken lightly.
Categories Explained
Now, onto the nuts and bolts. Treating the defect types above as guidelines, we’ve compiled the following categories in ascending order of severity.
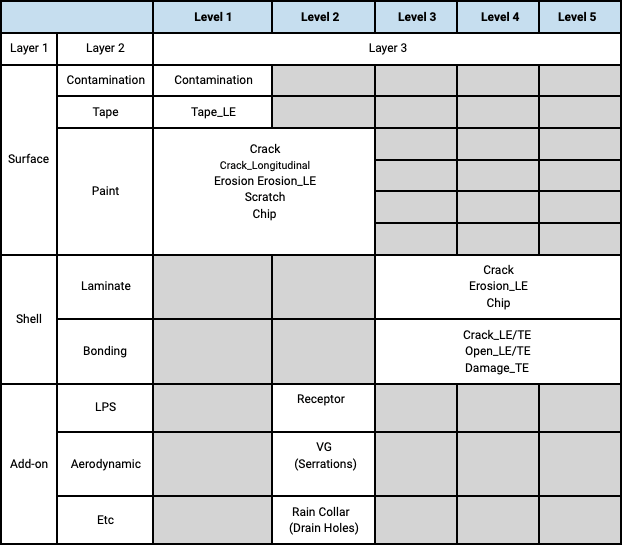
Severity 1
- Surface (coating/paint/tape) discoloration, flaking, and contamination (dust, wet spots, insect debris)
- Surface (coating/paint) damage (chip, crack, erosion, scratch, etc.), excluding laminate exposure
Severity 2
- Surface (coating/paint) damage (e.g., chip, crack, erosion, scratch, etc.), including laminate exposure
- Damages to add-on accessories (LPS, VG, rain collar, drain holes, etc.)
Severity 3
- Low-grade damage (chip, crack, erosion) to the laminate and juncture connecting leading and trailing edges (bonding)
- Laminate crack (~200mm and under)
- Bonding crack (~500mm and under)
Severity 4
- Acute damage (chip, crack, erosion) to the laminate and bonding
- Laminate crack (over 200mm)
- Bonding crack (over ~500mm and under 1000mm)
- Bonding open (under ~100mm in size and spotted within a five-meter range from the tip)
- Bonding open (under ~ 200mm and spotted outside of beyond, a five-meter range from the tip)
Severity 5
- Critical damage (chip, crack, erosion) to the laminate and juncture connecting the bonding
- Splitting of the shell from laminate crack (all shapes and sizes)
- Bonding crack (1000mm and over)
- Laminate/Bonding open (over ~100mm in size and spotted within a five-meter range from the tip)
- Laminate/Bonding open (over ~200mm in size and spotted outside of a five-meter range from the tip)
- Buckling
Final Words
From tiny surface scratches and indiscernible dust stains to egregious rifts and thunderous lightning strikes that wreak havoc, each defect comes with its own set of challenges.
Through diligent inspections and prompt maintenance, as illustrated through NearthWIND Pro and Mobile, we’ve empowered blades to continue their noble mission of bringing a greener tomorrow. Now with detailed yet comprehensive standards under our belt, the future of blade O&M will come to shine brighter than ever.
Looking to get a feel of how defect categories will come to revolutionize your O&M game? Connect with one of our specialists today to get on Zoomable for a firsthand experience.